Building a better box: Green Bay Packaging embraces innovation
Green Bay Packaging, founded in 1933 by George and Marguerite Kress, is a leader in innovation and sustainability within the manufacturing industry.
Starting with a single box plant in Green Bay, the company has expanded to more than 40 locations nationwide. As a proud family-owned and American-made manufacturer, it is dedicated to leading the industry with an award-winning commitment to sustainable manufacturing practices.
The Green Bay Packaging Mill Division has a history of innovation and sustainability.
In 1948, George Kress established the Green Bay Pulp and Paper Mill, now known as the Green Bay Packaging Mill Division. This mill was built to produce a semi-chemical corrugated medium for the box plant.
In 1957, two decades before recycling became mainstream, the Green Bay Mill began collecting old, corrugated containers to create this medium. In 1973, the company won a gold medal award for efforts in water pollution abatement. By 1991, the mill was redesigned to produce high-performance containerboard using 100% recycled fiber, discontinuing the use of virgin pulp. In 1992, the mill became one of first in the world to be totally effluent-free.
Technology fuels sustainability
In 2017, the leadership of Green Bay Packaging held an important meeting to discuss the future of the Green Bay mill. Although the mill had been updated several times since 1948, it was approaching the end of its useful life.
The company considered the options: it could continue operating the mill until it became inoperable; move to the lower Midwest where logistics were more advantageous or construct a new, high-performance recycled paper mill at the original site on North Quincy Street, near the mouth of the Fox River.
In 2018, Green Bay Packaging invested more than $600 million to build a new state-of-the-art paper mill, which became Wisconsin’s first paper mill in more than 30 years.
“Will Kress, the chairman and CEO of Green Bay Packaging, is deeply committed to the Green Bay community and our dedicated employees; thus, the decision was made to build the new paper mill in the same location,” said Bryan Hollenbach, executive vice president at Green Bay Packaging.
Looking to the future, the new state-of-the-art facility was designed with cutting-edge equipment that enhances the company’s capabilities and operational efficiencies to better serve its customers.
“We are dedicated to our industry, employees, and customers,” Hollenbach added.
The mill is the most sustainable paper mill in North America. The innovative, energy-saving technologies integrated into its design have resulted in an 11% reduction in energy usage per ton of paper produced and a 35% reduction in greenhouse gas emissions per ton. Additionally, the mill uses two natural gas boilers and captures 100% of the biogas from the anaerobic digester wastewater treatment to generate renewable energy. This state-of-the-art biogas generator produces electricity used in the manufacturing process.
The mill’s circular reclaimed water system, recognized by Underwriters Laboratories as the world’s first Net Zero Water facility, underscores the commitment to technical innovation. With its groundbreaking design, the mill utilizes water that would have otherwise been discharged back into the Lake Michigan watershed by the local municipal water treatment plant, transforming a water-intensive process into a more water-resilient operation. The Green Bay mill neither pulls water from nor discharges water into the adjacent Fox River.
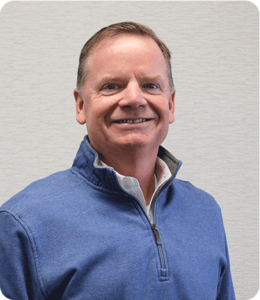
Bryan Hollenbach
A promising future through planning and design
To support one of the largest economic development projects in state history, WEDC authorized up to $60 million in performance-based tax credits for the state-of-the-art project.
When the new mill opened in 2021, WEDC Secretary and CEO Missy Hughes praised the company’s investment, calling it “a testament to the strength of our state’s paper industry, which remains a major driver of our economy.”
Hollenbach expressed gratitude for WEDC’s collaboration on the project, stating, “Their support helped us navigate challenges and strengthened our communication with the Department of Natural Resources during the permitting process.”
Investing in the new mill enhanced Green Bay Packaging’s competitive positioning in the market and solidified its commitment to environmental stewardship.
“We are committed to reinvesting for future success,” said Hollenbach.